The choice of materials for ROVs depends on various factors, including the specific requirements of the ROV’s intended use, environmental conditions, operational depth, budget constraints, and more. Anodized aluminum is commonly used in ROVs for certain components, but it may not be the best choice for all parts of the vehicle. We discussed this in a previous post. In this blog, let’s compare anodized aluminum with other materials commonly used in ROVs.
Anodized Aluminum
Benefits. Anodized aluminum offers corrosion resistance, durability, and relatively low weight. Structural components, frames, and housings commonly consist of anodized aluminum, at least partially so. Its non-corrosive properties make the aluminum well-suited for use in marine environments. Its light-weight makes it great for ROVs. Lower weight = less thrust required (generally) = lower power requirement.
Shortcomings. While anodized aluminum provides corrosion resistance, it may not be suitable for extremely deep-sea applications where higher-strength materials like titanium are preferred. Additionally, anodized coatings can wear off under abrasive conditions.
Titanium
Benefits. Titanium is exceptionally strong, lightweight, and corrosion-resistant, even in deep-sea environments. It has excellent fatigue resistance and can withstand high pressures and aggressive fluids encountered in deep-sea operations. By deep-sea, we mean really deep. Beyond the SEAMOR Marine depth limit of 600m / 1960 ft.
Shortcoming. Titanium is more expensive than aluminum, and its fabrication can be more complex. It’s often used for critical components like pressure housings and structural elements in deep-sea ROVs. Titanium is a necessary material for deep-sea ROVs, however, the complex fabrication process, higher price and larger environmental footprint than anodized aluminum, often disqualifies the metal from use in other ROVs.
Stainless Steel
Benefits. Stainless steel is corrosion-resistant and offers good strength. It’s suitable for components that require high strength and resistance to corrosion, such as fasteners, connectors, and certain structural parts. This metal is another one of SEAMOR favourites. We need it for its strength as it improves the durability of our ROVs.
Shortcoming. Stainless steel is heavier than aluminum and titanium, which may impact the ROV’s buoyancy and overall weight. It may also require additional surface treatments for optimal corrosion resistance.
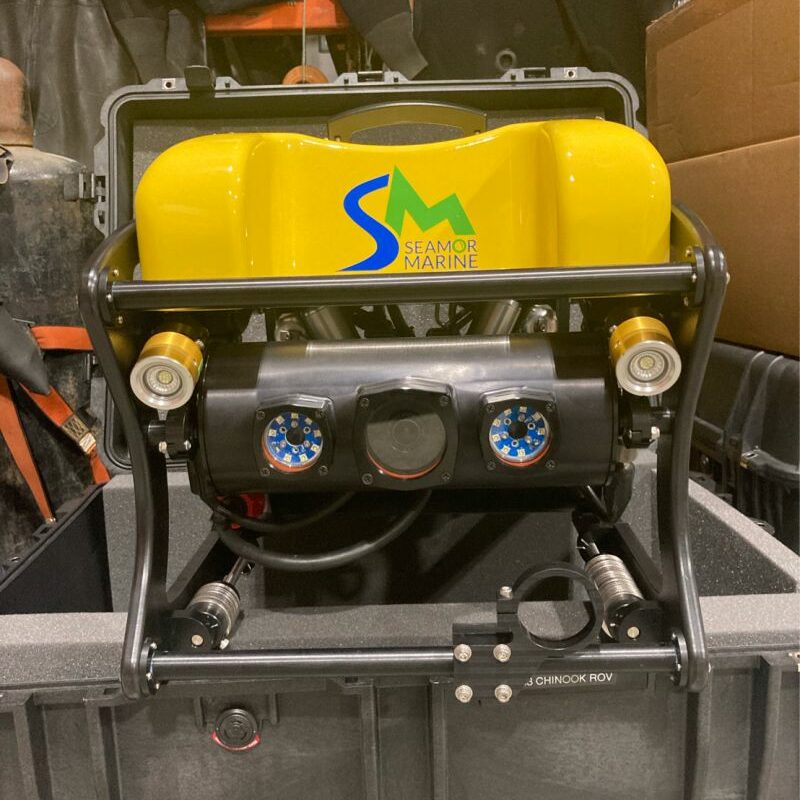
Plastics and Composites
Benefits. Plastics and composites can offer a good balance of strength, weight, and corrosion resistance. They are often used for components where weight savings and insulation from electrical conductivity are important. Plastics are great seals and prevent water from seeping into places it should not be.
Shortcoming. Plastics and composites may have limitations in terms of depth capability and high-temperature resistance. They might not be suitable for certain deep-sea or high-temperature applications. When an ROV is predominantly made of plastic, be sure to double-check your ROV needs with the capabilities of the model. Ask for an in the field demo. SEAMOR Marine uses some marine-grade polymers but it is not our material of choice for many of our components. We simply need a higher-quality ROV materials to guarantee our models are an investment in your business rather than a cost.
Ceramics
Benefits. Ceramics can provide excellent corrosion resistance, wear resistance, and thermal stability. They are suitable for certain specialized applications such as sensors, bearings, and high-temperature components. They’re worthy of being listed because they are used in many different ROV accessories. However, you’ll rarely see ceramics in the body of an ROV.
Shortcoming. Ceramics can be brittle and may require careful engineering to prevent failure under mechanical stress or impact. Out of all the common materials for ROVs, ceramics is the least versatile and requires the most effort to make it work.