There is no single definition of what inspection class ROVs are. However, we can give you an overview of the most important attributes of the best inspection class ROVs. In short, your ROV needs to get the job done. In reality, your ROV needs to repeatedly, reliably, and easily get the job done. We all know the more reliable the ROV, the more down time you can avoid, the more jobs you can do in a day, and the more profits a business can make. Don’t be fooled into picking the ROV with the lowest upfront cost if it doesn’t come with the long-term promise and the necessary on-going customer support.
Modularity
- Cost Savings on Equipment. Modular ROVs can be configured with different payloads and sensors to suit specific inspection requirements. Instead of purchasing multiple specialized ROVs for different tasks, having one modular ROV to do the job saves time and money.
- Reduced Downtime and Operational Costs. Modular ROVs offer flexibility in adapting to changing inspection needs. If a component fails or requires maintenance, it is easily fixed or replaced, minimizing downtime. This reduces the loss of revenue associated with equipment downtime and lowers operational costs by streamlining maintenance procedures.
- Scalability and Future-Proofing. As inspection needs evolve or new technologies emerge, modular ROVs can be upgraded or reconfigured to accommodate these changes. This scalability allows your business to future-proof its inspection capabilities. You do not have to invest in entirely new ROV systems. By avoiding frequent replacements of outdated equipment, businesses can achieve long-term cost savings and maximize the return on their investment in ROV technology.
Ease of Use
- Maneuverability. Inspection class ROVs need to navigate through complex underwater environments with precision. They should be agile and capable of maneuvering around obstacles and tight spaces.
- Stability. Maintaining stability is crucial for capturing clear images and videos. It also helps with not crashing into something. The shape, material choices, thruster placement, etc., all aid in maneuverability and stability of ROVs. At SEAMOR, we use exact thruster placement, balanced payload placements, and quality materials to provide you with reliable and easy to use inspection class ROVs.
- Camera Quality. High-definition cameras with low-light performance are essential for capturing detailed images and videos, enabling accurate inspection.
- Visibility. Underwater environments are often dark, so powerful LED lights are necessary to illuminate the inspection area effectively. In murky waters, sonar systems and other non-visibility related sensors are a must.
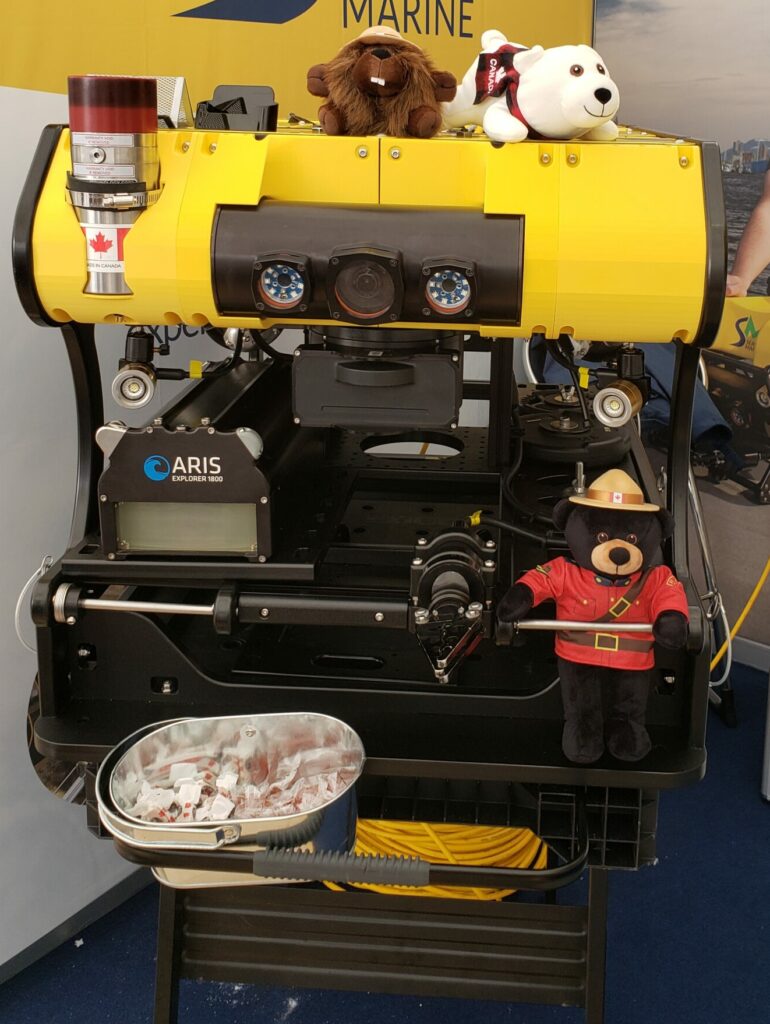
Lifespan
- Payload Capacity. ROVs may need to carry additional equipment such as sensors, manipulators, or tools for specific inspection tasks. Sufficient payload capacity ensures they can carry necessary gear.
- Power and Endurance. Longer battery life or the ability to be tethered to a power source ensures that ROVs can operate for extended periods without interruption.
- Safety Features. Built-in safety features such as fail-safes and obstacle avoidance technology help prevent accidents and protect the ROV from damage.
- Compatibility and Integration. Compatibility with other inspection equipment and software systems facilitates seamless data analysis and reporting.
Customer Support
- Operational Efficiency and Reliability. Effective customer support means operators receive timely assistance in resolving technical issues or troubleshooting problems with their ROVs. This minimizes downtime so inspection operations can proceed smoothly, maintaining operational efficiency. Quick resolution of issues also contributes to the reliability of the ROV, enhancing overall performance and productivity.
- Maximizing ROI and Longevity. Inspection class ROVs are significant investments, and organizations rely on them to fulfill critical underwater inspection tasks. Comprehensive customer support services, including maintenance guidance, repair assistance, and access to spare parts, help maximize the return on investment by prolonging the lifespan of the ROV. By making sure your ROV remains operational and well-maintained, SEAMOR customer support contributes to the longevity of your ROV and the quality of your business.
- User Training and Knowledge Transfer. Training programs and resources to educate operators on the proper use, maintenance, and troubleshooting of the ROV. Well-trained pilots can fly the ROV more effectively, reducing the likelihood of accidents or damage during inspections. Additionally, knowledge transfer initiatives empower operators to leverage the full capabilities of the ROV, enabling them to conduct more thorough and accurate inspections. This ultimately leads to better outcomes and enhances the overall quality of inspection services provided to customers.
It goes without saying that SEAMOR ROVs have all of these qualities making them the best choice for your business. Get in touch to learn more or to get your hands on your very own SEAMOR ROV.