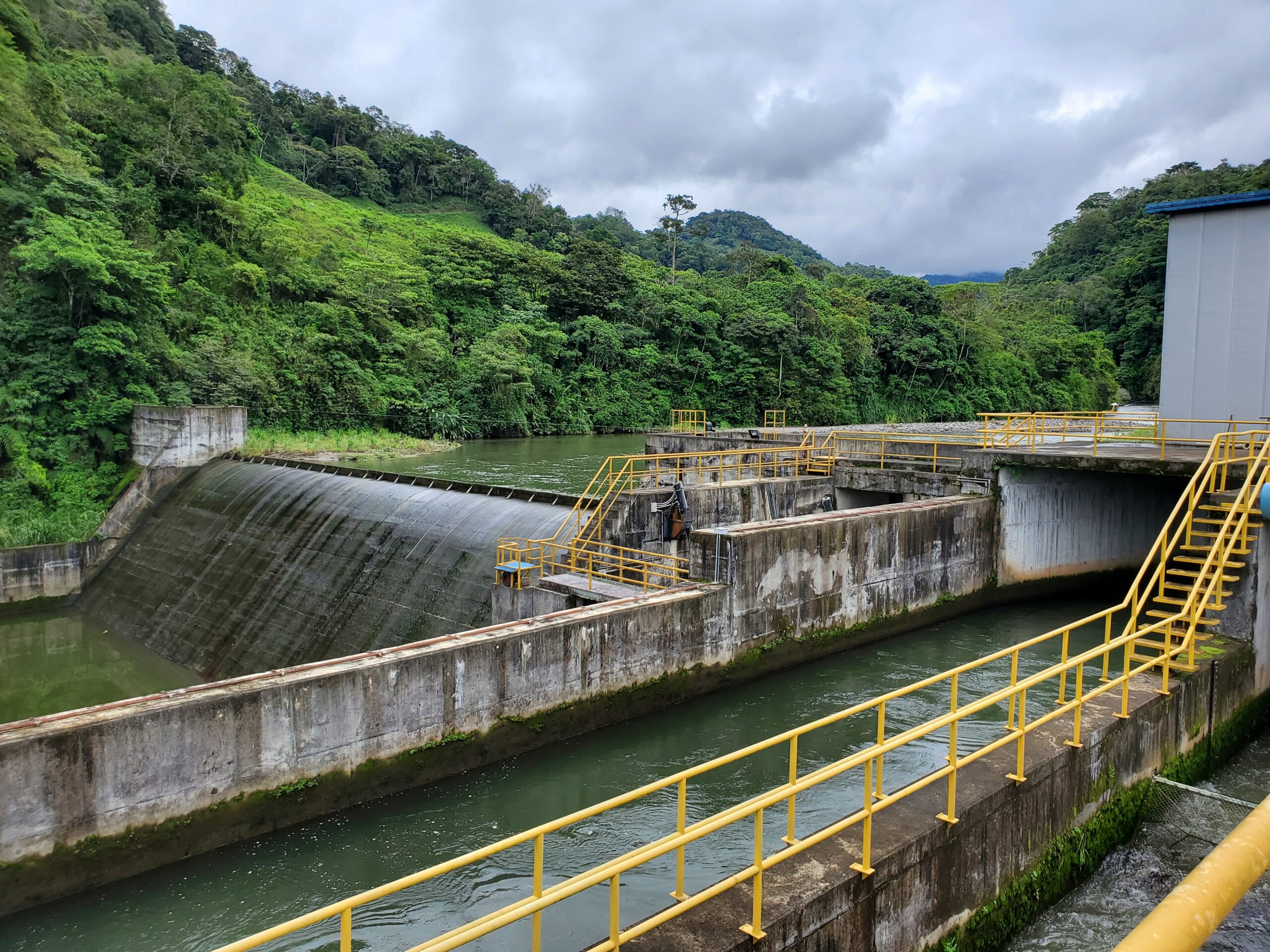
Long-range tunnel inspections by SEAMOR’s Chinook ROV improve cost efficiency and minimize environmental impact at hydroelectric power plant in Panama
Situation
Panama’s hydroelectric generation company, Electron Investment SA (EISA), needed to inspect 5 kilometers of tunnel and 2 kilometers of penstock at its Pando hydroelectric power plant on the Old Chiriqui River to identify any areas in need of repair. EISA had two options: either do a dry inspection after lowering the lake portion and draining the tunnel or use an underwater ROV for the inspection.
To do a dry inspection, EISA would need to remove 10,000 cubic meters of water from the tunnel and empty the lake, a difficult and time-consuming process. It would take about two weeks to empty the tunnel and be able to access it by foot. The cost of that process is already high, but the higher cost is the loss of power generation. The people of Panama rely on the power plant for their electricity, and interruptions in service can be devastating. There is also an environmental factor that comes with emptying and filling the tunnel again, even if done only partially. Instead, EISA opted to purchase SEAMOR Marine’s Chinook ROV and 3-kilometer fiber optic tether and reel system for the inspection.
Problem
Inspecting this 5km long tunnel came with several challenges. Because of problems with excavation, the tunnel goes down, then up to a vertical shaft, and then down again to the powerhouse with its low point at about 500 meters into the tunnel. Poor visibility was another factor. This area of Panama is volcanic with lots of silt and organic matter in the water, which can create near-zero visibility.
Solution
For the inspections, EISA used a Chinook ROV and 3-kilometer fiber optics tether. Able to dive to 600 meters (2,000 feet), the ROV was equipped with a sensor skid carrying two Imagenex sonars: the 965A digital multi-beam imaging sonar and the DT360 multi-beam profiling sonar. These sonars were operated simultaneously using an Ethernet switch to the fiber optic tether multiplexer, allowing the EISA team to navigate and inspect tunnel walls in almost zero-visibility conditions. Auto depth and auto heading functions helped EISA safely navigate the tunnel, which had two access points.
Results
“One of the main reasons we chose an ROV to inspect the tunnels was that it was much less costly both financially and environmentally than the alternative of draining the tunnels for inspection,” said Iván Parra, Civil Engineer at EISA. “The operation was completed with a very small environmental footprint using SEAMOR technology and expertise.”
It was the first-time engineers from EISA had piloted an underwater ROV, and all went smoothly.
“We like the ease of use. It is pretty easy to control, almost like flying a drone,” says Parra. “It’s very user friendly. The connections are also user friendly. Each connector has a different number of pins, and they are all clearly labelled. It makes it easier to connect all the components.“
Both the depth rating of the ROV and the capacity to change the tether length were important for EISA when making the decision to purchase the Chinook, says Parra. He said sometimes you don’t want to be moving a big 3km reel just to inspect the intake; you need a 200m reel you can handle by yourself. That modular capacity was very important to EISA.
The EISA team has already begun to use the Chinook ROV for other tasks, serving the local hydroelectric generation industry with state-of-the-art technology. EISA recently used their SEAMOR Chinook ROV to inspect the trash racks by the intake when it was obstructed with floating debris. It also meets EISA’s other site needs, which include a property that has a 500 meter deep lake.
“It worked flawlessly,” says Parra.
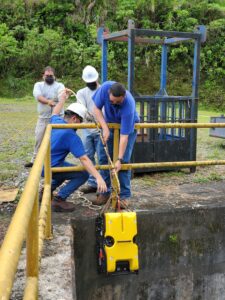