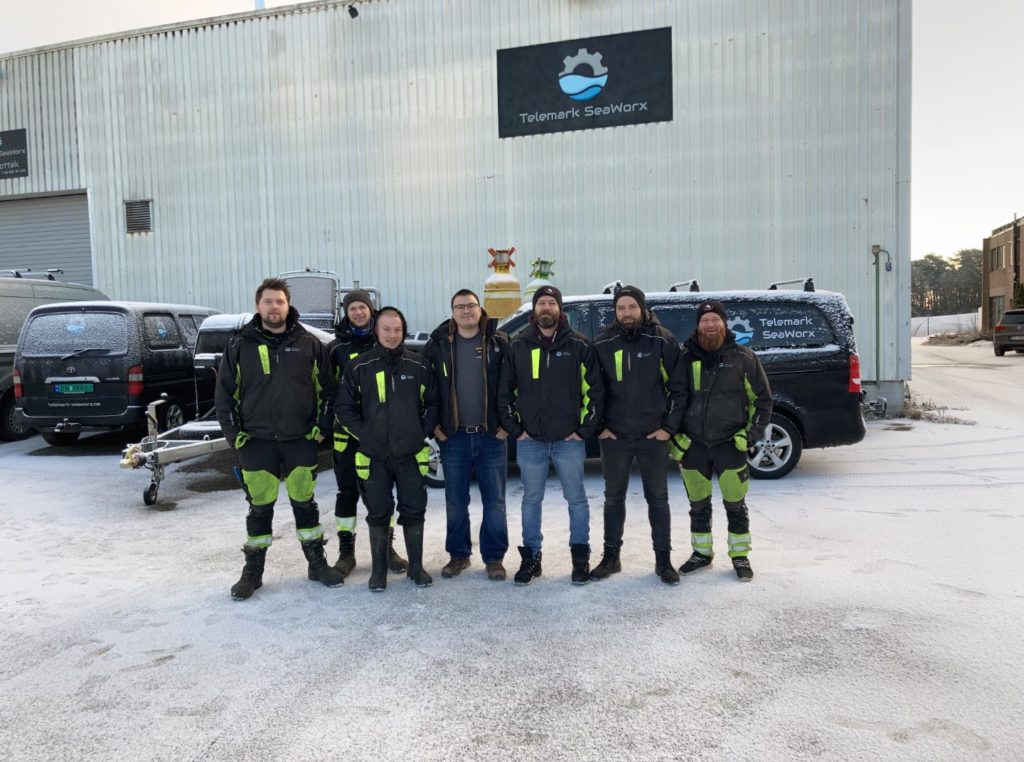
Situation
Underwater contractor Telemark SeaWorx in Langesund, Norway, uses a SEAMOR Chinook ROV for several underwater applications including inspections, moving power lines, searches, and seabed mapping. The company contacted SEAMOR’s service department directly when issues repeatedly arose with their ROV.
Problem
Telemark SeaWorx had problems with their Chinook ROV that cropped up over several months: the auxiliary camera stopped operating in colour, the main camera stopped displaying a picture, and the control panel had stopped working with some controls. After these initial problems were dealt with the system suffered a critical failure shortly after being returned to the client. This damage was at the vehicle and caused a complete loss of control and power to the vehicle. After this problem was resolved the client suffered a further setback with a burnout of the deck cable connector at the loaner tether reel we provided (see solution section). A second deck cable, along with the client’s now repaired tether reel, suffered a similar failure resulting in loss of controls and videos. Damage to the deck cable at the reel was detected in the same position as before.
Solution
We addressed the first repair issue by asking Telemark to ship the malfunctioning system to our Service Department, where it was repaired, serviced, and returned. When problems quickly occurred again, we arranged a video call that very night to provide remote support and analysis. We provided alternative parts and a loaner reel for urgent delivery to resolve the problem. When further problems promptly arose, we provided additional support. After the system was confirmed working, the problem occurred again. At this point we realized that since no ROV dealer was able to support Telemark, an onsite visit by our service technologist was necessary. During our in-person inspection, we made the repairs and shared with the team some best practices for ROV maintenance, and Telemark hasn’t had any problems since.
Here are more details;
Telemark shipped the ROV to SEAMOR for the initial repair of the malfunctioning video camera. SEAMOR’s service technologist discovered that the issue was due to the incorrect installation of an after-market auxiliary light directly behind the electronics canister. When Telemark had installed the light, they relocated the lower thrusters, which was a reliability concern. Our service technologist remounted the auxiliary light with a crossmember assembly and moved the lower thrusters into the correct position to get the cameras working properly. A potentiometer was replaced in the controller along with a new power button. All of the thrusters were serviced and the tether was re-terminated with a fresh 16 pin cable.
A month later, the system suffered catastrophic failure during a dive in which the 16 pin cable and mating bulkhead exploded. We provided emergency remote support via a video call to identify the cause. Then we shipped the necessary replacement parts and a loaner reel to Telemark.
Shortly after the loaner arrived and was in use an explosion occurred at the deck cable where it connects to the reel.
The loaner reel was damaged beyond remote repair capabilities. Another deck cable was shipped to the client so they could resume work with their newly repaired reel. Shortly into use of their original reel the same problem occurred again. We communicated with the client and resolved to send our service technologist to Telemark in Norway to verify the issues and make the repairs onsite.
The onsite inspection revealed that the grease being used by Telemark was contaminated with conductive material and coagulated from being out of date. This is what caused the initial explosion with the 16 pin cable at the vehicle. Our service technologist also inspected the two damaged deck cables. Because they had been stored outside of the boat cabin between jobs, water and moisture in the air contaminated the dry-mate connectors allowing a short circuit to occur when the cables were plugged into the reel again. The first spare deck cable sent to the client was more susceptible to this contamination due to some greasy substance present on the connector ends.
SEAMOR’s service technologist made the repairs and shared maintenance tips to help Telemark avoid ROV malfunctions in the future, and Telemark hasn’t had any problems since. We do everything we can to support our customers so they can be successful in the ways they serve others.
Results
“Everything went as well as we could hope for. Thanks for providing such good support! Graeme is really good at what he does and knows the ROV well. Your customer service brought back our confidence of the Chinook ROV and we learned a lot. Thank you for your good support,” said Anders Melfald, CEO at Telemark SeaWorx.
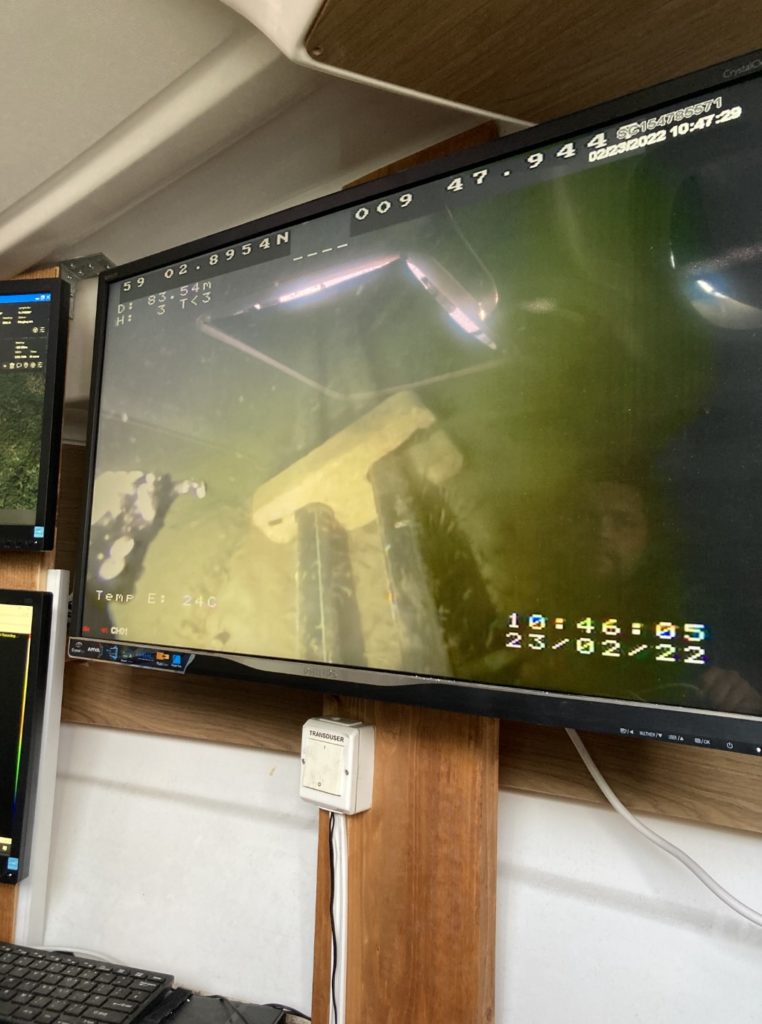
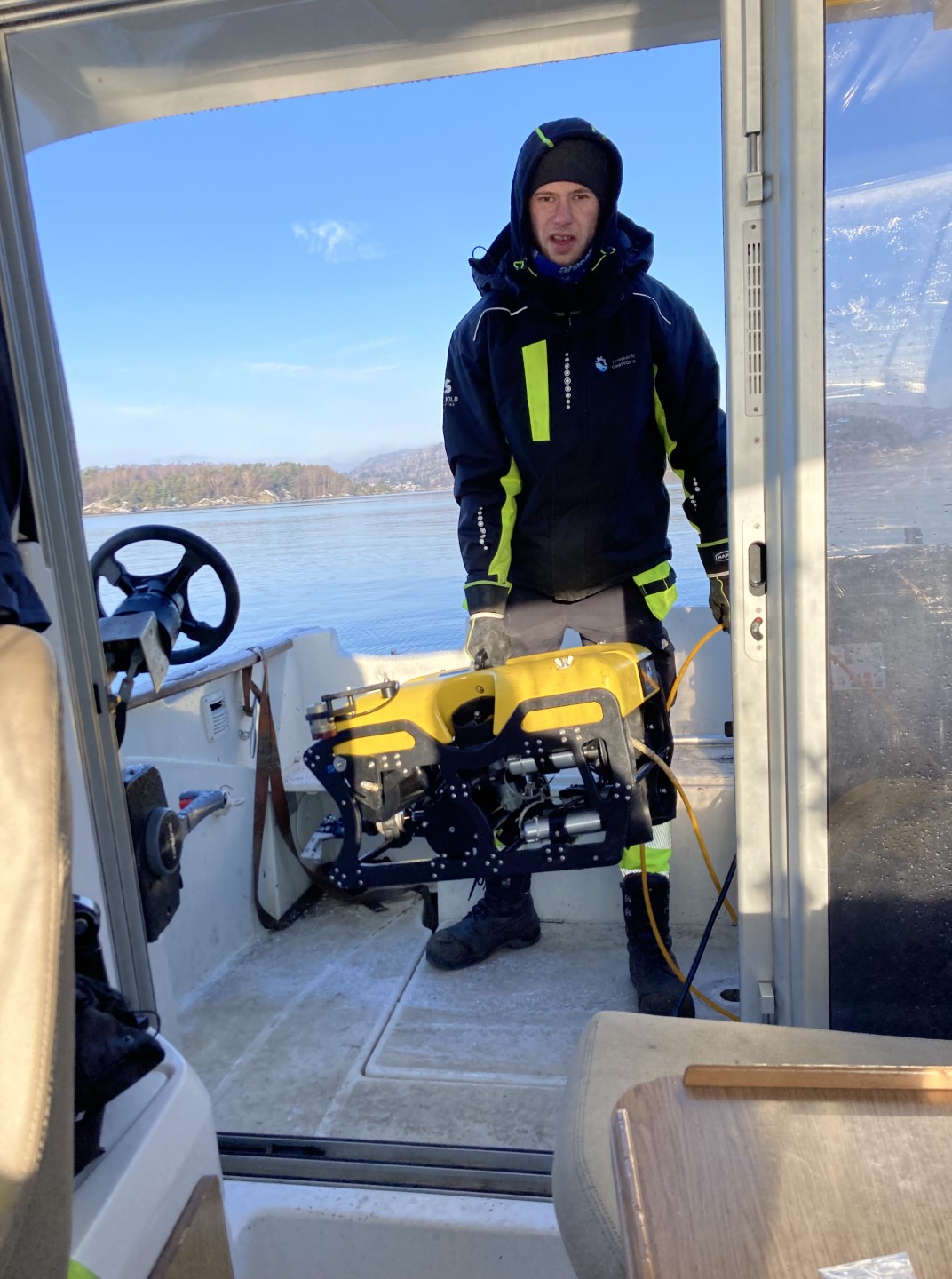
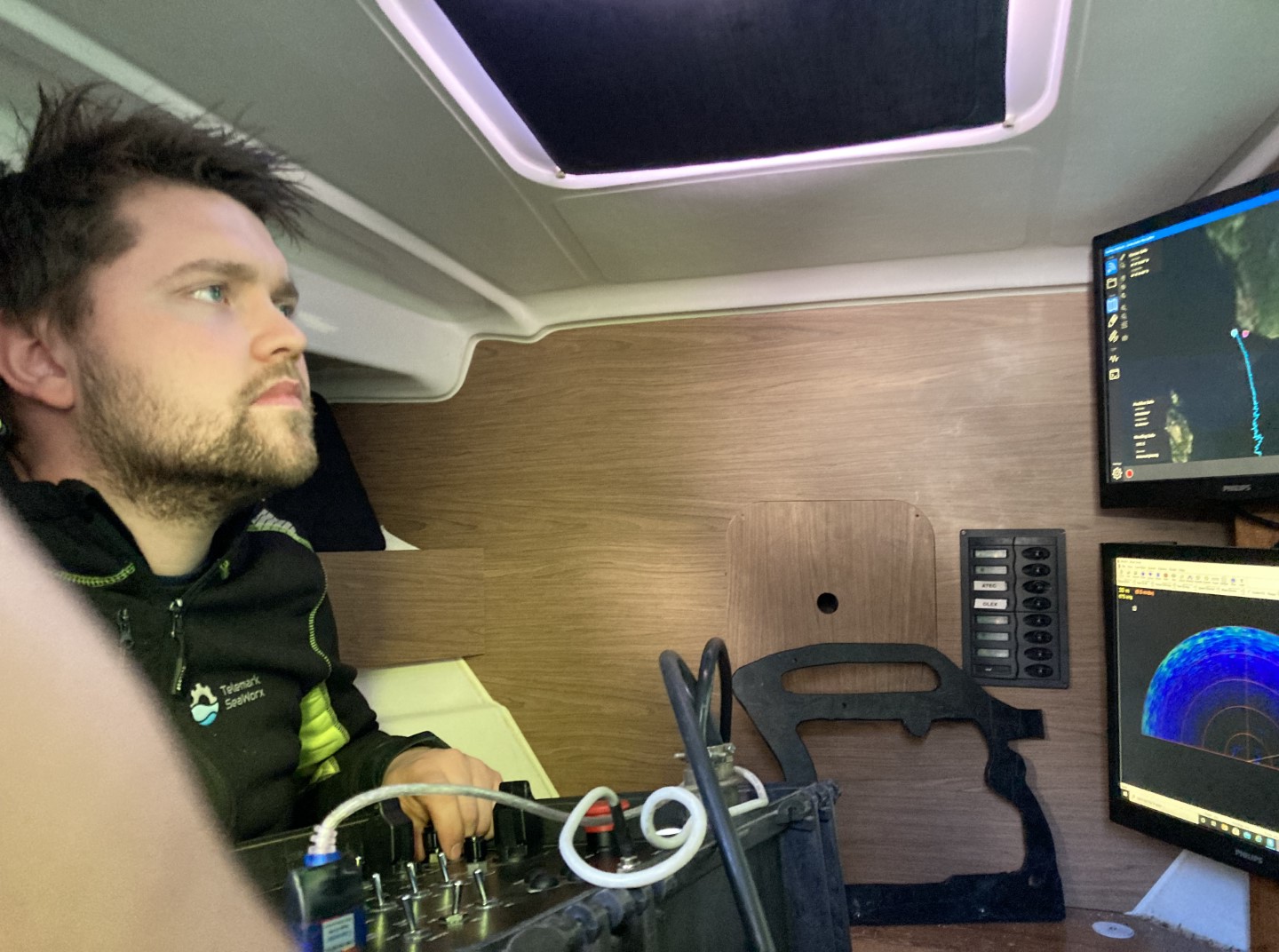